Quality Policy
Purpose
The KOKUSAI ELECTRIC Group (“KE Group") has established the following quality policy aiming to provide customers with high-quality products and services that support a future where creativity and innovation are born, under the slogan “Technology & Tai-wa for Tomorrow" as stated in the KOKUSAI ELECTRIC Way, which is KE Group’s corporate philosophy.
Basic Policy
KE Group supports a future where creativity and innovation are born by providing technologies that exceed society’s expectations and high-quality, competitive products and services.
(1)We achieve quality that earns the trust and satisfaction of our customers.
(2)We provide competitive products and services to our customers on time.
(3)Officers, employees, etc. perform their respective duties with sincerity, in accordance with applicable national laws and regulations, as well as basics and ethics, and think and act from the customer’s perspective, striving for continuous improvement.
Basic Activity
In accordance with the basic policy set forth in the preceding article, KE Group implements and thoroughly enforces the activities stipulated in the following items.
(1)We maintain quality transparency through constant Tai-wa with stakeholders.
(2)We provide products and services that meet customer’s needs and achieve higher customer satisfaction.
(3)We establish and maintain an appropriate quality control system in the supply chain.
(4)We comply with applicable national laws and regulations, industry standards, and customer requirements.
(5)We continually review our work procedures to improve the quality of products, services and operations.
(6)We continue to educate our officers, employees, etc. so that they understand the importance of quality and can put in into practice.
Ensuring Quality
ISO 9001 Certification and Quality Management System
The KOKUSAI ELECTRIC Group production sites have acquired ISO 9001 certification. We have built a quality management system based on a PDCA cycle using a process approach, and continuously make improvements.
Activities to Maintain and Improve the Quality Management System
Quality Management System (QMS)
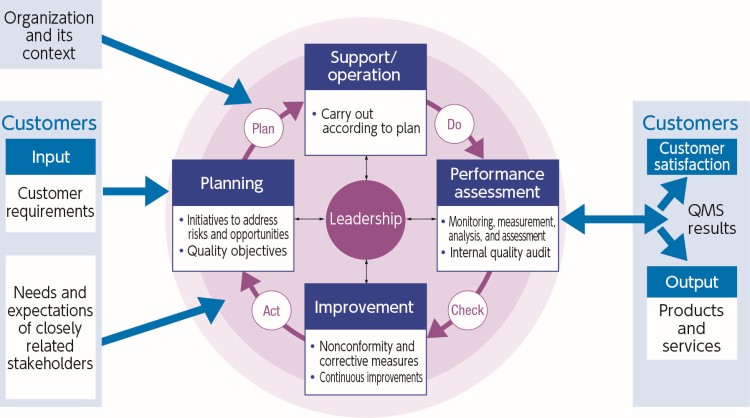
We strive to improve the quality of products and services by creating training programs to boost each employee’s quality assurance skills, carrying out company-wide activities to foster awareness on quality, and exchanging personnel involved in quality assurance and supporting their activities, which includes group companies and business partners.
Policy to Address Quality Problems
When a defect is discovered, we search thoroughly for the technological cause and the motivational factor that lies behind it, and work to prevent recurrence.
Moreover, we hold the Quality Meeting as necessary, where responsible departments report to management and relevant departments on measures to prevent recurrence, to disseminate information and improve quality, thereby improving technology and preventing quality problems.
Activities to Raise Quality Awareness
We created an e-learning program featuring case studies of quality problems, which is provided to all employees to share information and raise quality awareness.
In addition, every November is designated as “Quality Month,” a time when we focus on raising quality awareness throughout the company. Activities during Quality Month include display of examples of quality problems, distribution of messages on quality from departments, and display of quality slogans and senryu poems solicited from employees.
Enhancement of Customer Satisfaction (CS) Worldwide
We have been conducting an annual CS survey on our products and services covering customers worldwide, jointly with Group companies. After the responses are compiled and analyzed, the results are conveyed internally and shared with Group companies to make improvements and enhance customer satisfaction.
We strive to respond promptly to customer complaints and requests, analyze them, and share them internally.